In the quest for sustainable packaging solutions, pressed pulp packaging emerges as a standout option. Derived from natural and renewable resources, this type of packaging not only minimizes environmental impact but also meets the functional needs of modern consumers and businesses. This document explores the advantages, applications, and production process of pressed pulp packaging.
Advantages of Pressed Pulp Packaging
- Environmental Benefits:
- Biodegradability: Pressed pulp packaging is fully biodegradable, breaking down naturally without leaving harmful residues.
- Recyclability: It is made from recycled materials and can be recycled again, creating a closed-loop system.
- Reduced Carbon Footprint: The production process of pulp moulding machinery emits fewer greenhouse gases compared to plastic and other non-renewable materials.
- Material Properties:
- Durability: Despite being lightweight, pressed pulp packaging is strong and can protect products effectively during transit.
- Versatility: It can be molded into various shapes and sizes, accommodating a wide range of products.
- Thermal Insulation: It offers good thermal insulation, making it ideal for temperature-sensitive items.
- Economic Benefits:
- Cost-Effective: Utilizing recycled materials often reduces costs, and the simplicity of the production process can lead to further savings.
- Consumer Appeal: Growing environmental awareness makes eco-friendly packaging a selling point, potentially increasing market share.
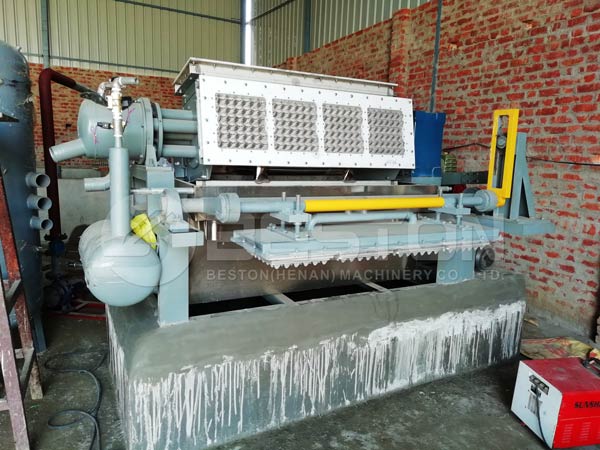
Applications of Pressed Pulp Packaging
- Food and Beverage Industry:
- Egg trays from egg tray machine
- Fruit trays
- Takeaway food containers
- Consumer Electronics:
- Protective packaging for devices
- Inserts and trays
- E-commerce and Retail:
- Custom packaging solutions for various products
- Void fillers and cushioning materials
- Healthcare and Pharmaceuticals:
- Packaging for medical devices
- Protective trays for medicines
Production Process
- Pulping:
- Material Collection: Recycled paper and cardboard are collected and sorted.
- Pulping Process: The materials are soaked in water and mechanically or chemically pulped to break them down into fibers.
- Molding:
- Pulp Formation: The pulp is blended to a desired consistency and poured into molds. Different molds can form different paper packaging trays. Want to make tableware? You can see the pulp molding tableware machine.
- Water Extraction: Excess water is removed through pressing and suction, forming the basic shape of the packaging.
- Drying:
- Oven Drying: The molded pulp is dried in ovens to remove remaining moisture, ensuring rigidity and strength.
- Finishing: The dried packaging is trimmed and finished as needed, ready for use or further processing.
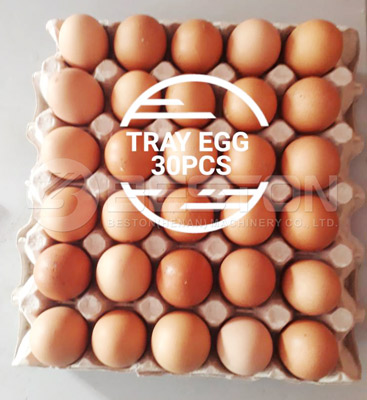
Conclusion
Pressed pulp packaging presents a viable and sustainable alternative to traditional packaging materials. Its environmental benefits, coupled with its functional versatility and economic advantages, make it an ideal choice for various industries. As the demand for eco-friendly solutions continues to rise, pressed pulp packaging is poised to play a crucial role in the future of sustainable packaging. Check the Beston Group here.