The responsible disposal of waste tires has become a major problem for the planet in recent decades as more cars have hit the roads and landfill sites are overflowing. In fact, one tire scrape yard in Kuwaiti can be seen from space. While tires can be burnt for fuel, the process produces a lot of pollution. The good news is that according to tyre pyrolysis project report and case studies, businesses in the waste tire disposal industry are now able to make healthy profits with a rubber pyrolysis machine designed for efficiency. And, pyrolysis is a process that, unlike incineration, does not produce any toxic emissions. See the tire pyrolysis project report now.
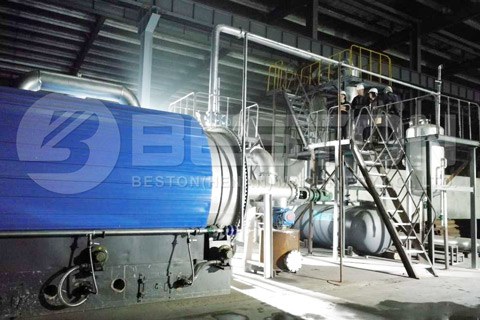
So, what sorts of commodities can be recovered from waste tires via pyrolysis? The answer is pyrolysis oil, steel wire, carbon black, and combustible gas. Pyrolysis oil is a thick fuel oil that can be sold unrefined or distilled into gasoline and diesel oil. Carbon black, meanwhile, is a sought-after product in many industries including the pharmaceutical, paint, tire manufacturing, and fertilizer industries. An average road tire is 35% carbon black, 45% tire oil, 8% combustible gas, and 12% steel wire. This means there are around 45 tons of fuel oil in 100 tons of scrap tires. Take the tyre oil machine to make oil.
When it comes to the price of a waste tire pyrolysis plant, it varies based on the plant type and the manufacturer. You can find batch, semi-continuous, and fully continuous pyrolysis plants for sale, and prices start at around $45,000 for an entry-level manual model. The downside of pyrolysis plants that utilize the batch working method is that they have limited daily capacities due to the requirement to cool down the reactor between batches. This cooling process can take up to six hours, meaning only one batch can be processed a day.
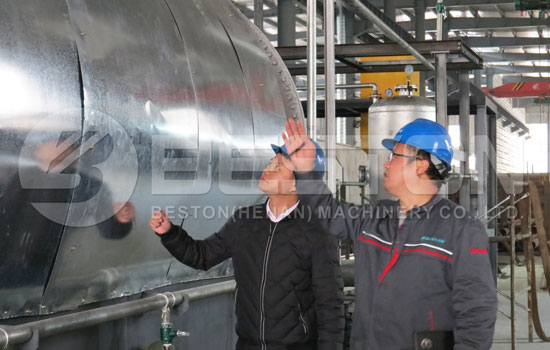
Meanwhile, a fully continuous pyrolysis plant can operate round the clock and process over 24 tons of waste tires a day owing to its automatic feeding and discharging systems. The reactor pattern style is also much more stable and efficient in fully continuous pyrolysis plants as it’s horizontal rather than 360-degree rotary like what is found in batch plants. By the way, get fair tire recycling machine cost.
A typically pyrolysis tire plant will last for a maximum of 8 years before the reactor requires replacement. To extend the life of the reactor, tire recycling businesses can remove steel wire from raw waste materials before feeding it into the pyrolysis machine. There are of course other pretreatment processes that are required for efficient pyrolysis. First, the tires must be ground up into small pieces. Fortunately, you can find tire shredders and automatic tire grinding machines in the marketplace to accomplish this task. Next, if the moisture content is greater than around 15%, the waste tires need to go through a drying machine.